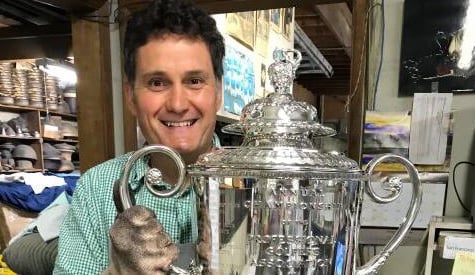
By Al Barkow
Engraving the winner’s name on a tournament trophy long has required a surgeon’s touch, but modern technology is making engravers a dying breed.
It may seem a little over the top, but it could be said that the person who engraves trophies with the names of the winners of tournaments and their scores is an agent of immortality. After all, the feat, like that of the champion golfer, will last forever. When that notion was mentioned to Ken Smith, a third-generation engraver now retired, and who did NCGA trophies for some 40 years, he says he was aware of that idea but prefers to “keep my ego in check on it.”
When the thought was brought up to Rick Biro, a silversmith in San Francisco who does the current engraving for the NCGA, he smiles, nods quietly, and says, “We are artisans and take a degree of pride in that we are perpetuating mortality. Our work honors an individual whose name will remain in memory forever, and the engraver is part of that.”
Nicely put.
However that may be, engraving goes back to caveman days, when early man chipped or carved out on the walls of his dwelling animal images, among other things that he encountered in life. Championship trophies are somewhat more sophisticated and is not a “carve” job. It asks for a surgeon’s touch, for sure, and an eagle-eye – steadfast attention to the information being fashioned. Indeed, Ken Smith served an eight-year apprenticeship with his father. Why so long? “My father was very meticulous,” says Smith, whose father learned the craft from his father, who was a sea captain in the 1880s and apprenticed with an engraver at age 19.
“My father took over grandpa’s shop and became a master engraver in 1952,” Smith notes. “He started teaching me in 1964.”
What’s to learn?
“There is as much precision as in any trade. The lines must be put on straight,” Smith points out. “No one will stand for anything being crooked. Getting them straight is not as easy as it may seem, especially when working on curved surfaces. You can lose control of the tool and it can slip across the metal. If a mistake is made it must be buffed out. There is block lettering, script lettering, Old English. Most trophies are block lettered, but in doing the name of the event there is going to be some curvature, cross-shading, double lines. And, a straight line on one side of a letter, curves on the other side; the letter B, for example.”
The process begins by putting a substance – Vaseline, grease, some sort of fat on the area to be engraved, then sprinkling that over with talcum powder. The information is traced on the powder and then the engraving begins. The tools used are called burins or gravers; or, if you are into the mundane, chisels. They are made of steel, have a lozenge-shaped point or tip, and are quite small – some the length of a middle finger.
Smith has also done all the trophies for The Olympic Club – club championships, senior championships etc. And the trophy for the 1998 U.S. Open played at Olympic. There was other work, as well.
“In 2014 Rick Biro got me to do the LPGA tournament at Lake Merced,” Smith recalls. “The Swinging Skirts was the name of the event. They wanted the engraver to come out to the course and at first it looked like Stacy Lewis would be the winner. I was prepared to put her name on the trophy, but Lydia Ko made a strong finish and won, and I ended up doing the engraving by flashlight.”
With that experience in mind, Smith remarked how he enjoys watching the British Open, when they almost invariably show the engraver working up the winner’s name and score in the minutes after the new champion is finishing his round. Perhaps a bit sooner if the leader is ahead by four strokes.
Alas, “classic” engraving, that which is done by hand, is a dying art. As Ken Smith notes, “In 1960, when I got into it, there were 10 or 12 hand engravers in San Francisco. Now there are maybe five or six. And there are no teachers to train new engravers.”
What is taking its place? Lasering. Although this method has been around for 40 or more years, it is now taking over much of the engraving business. It is less expensive, for one thing, and the work can be delivered more quickly. Furthermore, it doesn’t take nearly as long an apprenticeship to learn how to do the work on the laser machine. “In a year of doing it steadily, you’ll have the method down,” says Yuri Reis, of Aardvark Laser Engraving, in Oakland. The process is computerized, of course. The information, including font, letter size, is prepped onto a computer. The item – in our case a trophy – is positioned on the deck of the laser machine, a button is pressed, and there you have it.
Is there a difference in the final work between the two methods? Yes, albeit a very subtle one. It takes a certain aesthetic sensitivity to catch it. Lasering that is done on metals such as aluminum does not penetrate the surface. It lays atop it. Hand engraving digs in and thereby gives the information a greater significance by the mere fact of its depth. It looks like it will be there forever – or immortal, if you will.